Sublimation printing has revolutionized the world of custom apparel and textile design, offering prints that become part of the fabric itself. However, not all fabrics are created equal when it comes to this innovative printing technique. Choosing the right fabric is crucial for achieving the best results in dye sublimation printing.
This article will explore the top fabric choices for sublimation, delving into their properties, advantages, and ideal applications. Whether you’re a seasoned professional or a DIY enthusiast, understanding the best fabrics for sublimation will help you create stunning, high-quality prints that stand the test of time.
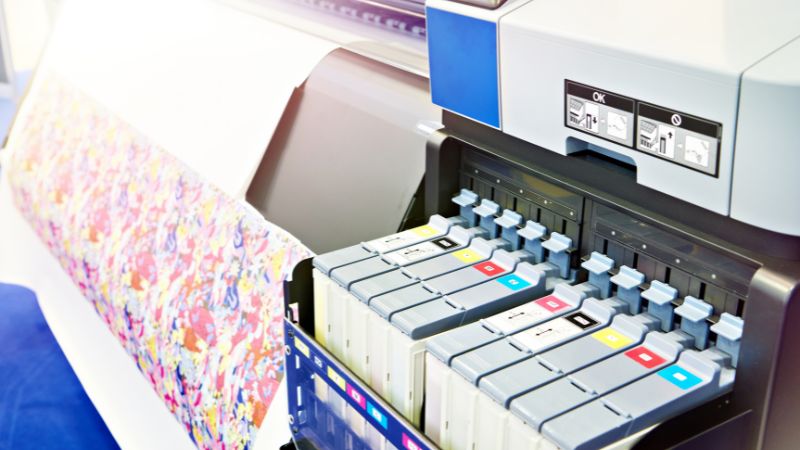
What is Sublimation Printing?
Sublimation printing is a digital printing process that uses heat and pressure to transfer dye onto materials.
Sublimation printing involves using a special ink that changes from a solid to a gas without becoming liquid. This method creates vibrant and permanent designs on various surfaces, particularly fabrics.
What Kind of Fabrics Are Perfect for Sublimation?
Sublimation printing works best on some types of fabric. Understanding which fabrics deliver bright, long-lasting prints can help you make the right choice.
Synthetic Fibers
100% Polyester is considered the best fabric for sublimation since polymers open up when exposed to heat, allowing the dye to enter and bond permanently. This gives you permanent and vibrant prints and remains largely wrinkle-free.
100% polyester fabrics ensure that designs are fully transferred, capturing every detail. The ink turns into gas and fuses with polyester molecules, resulting in vivid and colorful prints.
A high polyester content in your fabric also means your designs will stay bright longer. They won’t fade easily, even after many washes. This makes polyester ideal for sportswear, home décor, and promotional items. It’s also lightweight and breathable, which adds to its versatility for different uses.
Besides polyester, other synthetic fabrics like nylon, rayon, spandex and lycra can also be used. Their synthetic nature helps them react well with sublimation ink. However, polyester remains the most reliable.
Blends Fabric
It’s worth noting that while 100% cotton and other natural fibers are not ideal for sublimation, there are methods to treat these fabrics or use blends to achieve acceptable results, like blending them together.
Blended fabrics, such as poly-cotton blends (like a 65:35 or 50:50 mix), can also work well. These blends combine the durability and vibrancy of polyester with the softness of cotton.
What is the Sublimation Process on Different Fibers?
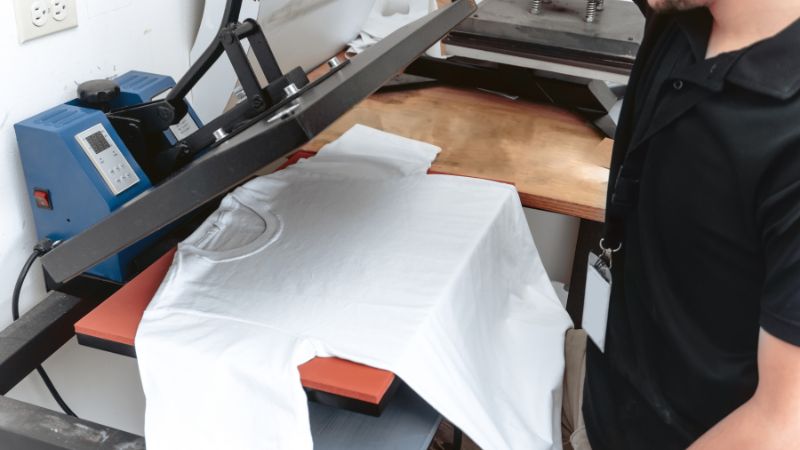
This section will explore how the sublimation process is applied to various fibers. However, before you begin the sublimation process, it’s essential to prepare your sublimation printer and familiarize yourself with the specific printing techniques and printing methods.
Normally, the sublimation printers are:
- Converted inkjet printers
- Dedicated sublimation printers
The method of sublimation dye includes:
1. All-Over Printing:
– Allows designs to cover the entire surface of a product
– Often used for apparel like t-shirts, hoodies, and sportswear
2. 3D Sublimation:
– Used for curved or irregular surfaces
– Requires specialized equipment like 3D vacuum heat presses
3. Multi-Step Sublimation:
– Used for complex designs or when printing on both sides of a product
– Involves multiple rounds of printing and pressing
100% Polyester
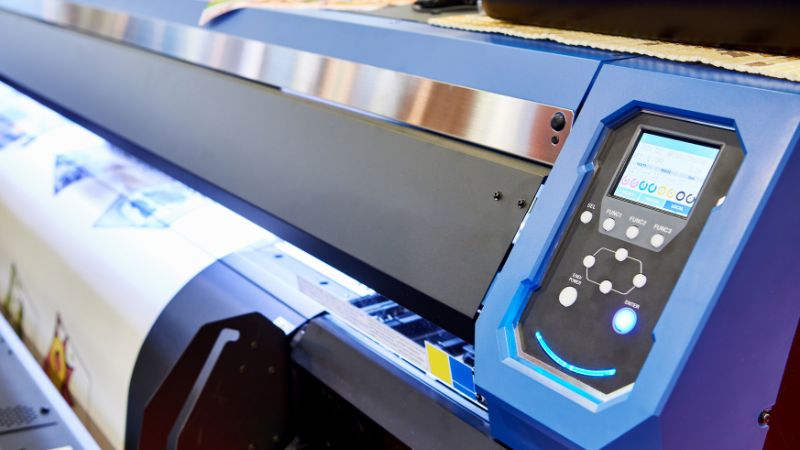
- Preparation: Ensure the polyester fabric is clean and wrinkle-free.
- Printing: Create the design and print it onto sublimation paper using sublimation inks.
- Heat Press: Place the printed transfer paper on the polyester fabric and apply heat (typically 350-400°F) and pressure for 30-60 seconds.
- Sublimation: The heat causes the ink to turn into gas, which then penetrates and bonds with the polyester fibers at a molecular level.
- Cooling: Allow the fabric to cool, then remove the transfer paper to reveal the permanent, vibrant print.
Polyester Blends
Here is the process of sublimating the blend polyesters, such as poly-cotton or poly-viscose.
- Fabric Content: The higher the polyester content, the better the sublimation results. A minimum of 50% polyester is recommended, with 65% or higher being ideal.
- Temperature: Use slightly lower temperatures (around 350-380°F) to prevent damage to the non-polyester fibers.
- Pressing Time: Adjust the pressing time based on the blend (typically 20-35 seconds).
- Expected Results: The non-polyester fibers won’t absorb the dye, resulting in a more muted, vintage look. For example, a 65/35 poly-cotton blend will have about 65% color saturation compared to 100% polyester.
Nylon
- Temperature: Use lower temperatures, typically between 330-340°F.
- Pressing Time: Apply heat for 80-90 seconds.
- Pre-treatment: Some nylon fabrics may need pre-treatment with additives to improve dye absorption.
- Type: Nylon 6 and Nylon 6,6 are the most common types used for sublimation due to their better color penetration and durability.
Spandex/Lycra
Spandex (also known as Lycra) is often used in blends for sublimation, particularly in activewear:
- Blending: Typically used in a blend with polyester (e.g., 80% polyester, 20% spandex).
- Temperature: Use temperatures similar to polyester blends (350-380°F).
- Pressing Time: Keep press times shorter (15-20 seconds) to prevent damage to the elastic fibers.
- Stretching: Pre-stretch the fabric on the heat press to ensure the design doesn’t distort when the garment is worn.
Acrylic
Acrylic fabrics can produce excellent results in sublimation due to their high polymer content:
- Temperature: Use higher temperatures, typically between 370-400°F.
- Pressing Time: Apply heat for 45-60 seconds.
- Type: Cast acrylic is preferred over extruded acrylic due to its higher heat resistance.
In conclusion, selecting the right fabric for sublimation printing is crucial for achieving vibrant, long-lasting results. While 100% polyester remains the gold standard for sublimation, offering unparalleled color vibrancy and print durability, other options like high-percentage polyester blends and specialized synthetic fabrics also provide excellent results for specific applications.